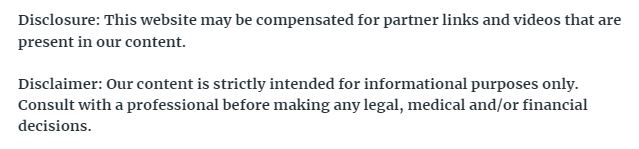
Manufacturing is enormous in the United States today, and many factories and automotive plants are hard at work building many different metal parts and devices from washing machines to cars to computers. But when a piece of metal is drilled, welded, or otherwise worked on, there may be metal burrs, or imperfections. The problem is that metal burrs often stick up and can make trouble for a device as long as they are present, so manufacturers have long since learned to remove them. This can be done with a carbide grinder, and carbide grinders are fed machines that will remove metal burrs with rapid rotation to grind off imperfections. A carbide grinder will remove metal burrs just fine, and this can make a piece of metal ready for use in everyday life. Machinist blocks can do similar work, and a tool set for mechanics can be touched up with a carbide grinder. What are some basic things to know about a typical carbide grinder today? What are the hazards of metal burrs?
A Carbide Grinder
It is with sheer scraping pressure that a carbide grinder will remove metal burrs from a piece of metal being fed into it, and this is not too different from how a power sander rapidly spins a surface to grind away imperfections on wood and similar materials. Power-fed machines may very in their rotating speed as they are fed material, ranging from 50 RPM to over 1,800 RPM. A low speed might sound it wouldn’t do a good job to a novice, but in fact, slower speeds do serve a purpose, and are useful for special operations. A lower RPM on a carbide grinder, for example, is ideal for counter-boring, counter-sinking, and reaming on the material being fed to it. In other cases, a metal burr simply must be bluntly ground off, and in some cases, a very high RPM will be best for the job.
Those who use such machines, however, should prepare everything ahead of time and adjust the settings so that a proper job can be done. One of the first things to do when preparing to grind a part is to tell the machine where “part zero” is. For those not aware, part zero is the datum that corresponds to the 0,0 coordinate on the CAD drawing. All CAM work involves a CAD drawing for generating the g-code part of the program. After all, today’s machines and factories have moved on from the days of the hand-operated, analog days of the 1800s. Today’s machines and tools have sensors and computers in them to perform more precise work, and many operations today have only a narrow range of what is considered acceptable work. Without programs inside the machines to tell them how to work, an unacceptably imprecise job may be done, and this can hamper production. Often, millimeters or even fractions of them can make all the difference. Workers today must make sure that their grinders, drills, and other tools are calibrated and set up just right for the work at hand.
Metal Burrs
As mentioned earlier, metal burrs often appear when a piece of metal has been worked on during manufacturing, and metal burrs cannot be allowed to remain on a piece of metal for long when they appear. Such burrs will cause problems for a device or appliance after it is built, and these burrs may, for example, cause scraping as parts in the product move. Such burrs can scratch the product while it is in use, or even cause snags that can harm motors as they strain to move the parts. In other cases, metal burrs might attract static electricity, and this can be a disaster for computers or similar parts. And in other cases, a person may get cut touching or scraping their skin against a a metal burr, and this can be a real source of irritation. Sloppy work involves leftover metal burrs, so manufacturers are careful to get them removed. One method for removing burrs is simply to use carbide grinders and their rapid rotation. As these machines are fed metal, they will rapidly grind away burrs and leave no trace of them at all.