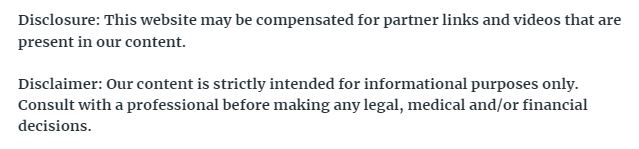
Reaction Injection Molding (RIM) is a process in which two liquid components are mixed and injected into a mold, where they then chemically react and cure. Common applications of RIM are the production of auto components (fenders, bumpers, etc.) and any other kinds of parts that need to be lightweight but durable.
The main advantages RIM has over the standard injection process are flexibility, strength and overall aesthetics.
Flexibility
The process used in RIM lends itself to greater flexibility and more design options. RIM uses low-viscosity liquid polymers, which facilitate chemical reactions that allow for expansion, thickening, and hardening in the mold. Engineers can more easily regulate the strength and density of the molded components. The process also requires less heat and energy than other methods and is more cost efficient as a result.
Strength
Compounds created in the Reaction Injection Molding process are microcellular systems, and they can have cells as small as 0.001 inches. The structure created in the RIM process lends itself to the creation of virtually unbreakable products. Compared to traditional injection molding, parts created through the RIM process will have a high weight-to-strength ratio.
In addition to being strong and durable, the lower pressures of RIM can allow for the encapsulation of things like sensitive electronic boards, without worry about damage. The lower pressures of the RIM molding process also allow for the encapsulation of a wide variety of materials in general.
In addition to being stronger, RIM products are about half as expensive to make as products made through other processes, like structural foam molding. Structural foam molding requires thermoplastic molds, which require higher pressure and are more expensive to use. There are similarities when talking about structural foam molding vs injection molding, but cost is one of the biggest advantages RIM has over other processes.
Aesthetics
Finally, materials created through RIM can be painted. They can also have silk-screen designs printed on them to represent a company’s brand image, making them attractive for reasons beyond their durability, strength, and cost.
It’s also worth noting that with a lower-pressure, lower-risk design process (meaning a finished product can be completed by RIM in the time it would take to create a prototype using other methods), there is more flexibility to perfect a design and make sure it matches the needs of the client without breaking the bank.