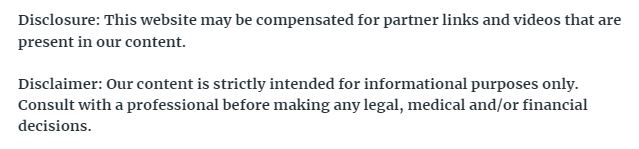
Generally, machining processes are meant to create a new shape of the material. Since metals are the most used substances in the manufacturing industry, machining process are generally carried out on metals. However, machining can also be carried out on other materials such are plastic that are also increasingly becoming popular. What happens is machining is that some material of the component is removed using a rotating cutter. A rotating cutter only forms part of the many types of burnishing tools. Typically, machining is carried out using a burnishing tool for metal that holds the workpiece in place during the process. In most cases, specific machining tools are used for a single kind of machining although there are flexible tools that can carry out more than one kind of machining to acquire enhanced dimensional accuracy. These tools can either be manual or automatic. Automatic machining tools tend to be more expensive as you also need to invest in a good control mechanism for their operation. Their major benefit is that the number of components that can be produced is relatively higher which brings down the labor cost. The speed at which machining tools produce finished components is dependent on the cutting speed as well as the efficiency in changing the components. There are flexible tools that allow automatic changing of the components but they also require substantive investment due to their efficiency.
Chip Removal and Chipless Machining Process
In machining, there are two major kind that are the chip removal process and the chipless machining method. Just like the name suggests, the chip removal process involves removing layers of metal in order to achieve the desired shape and dimensions of the parent metal. This is done by applying a compressive force on the metal so that a part of the material can be sheared off. Some of the most common chip removal processes include; drilling, bores, grinding, shaping and turning. The chipless machining method on the other hand does not include any form of chip removal. Using the chipless machining method, force is applied in order to achieve the desired dimensions and shape without any removal of material from the metal. Some of the most common forms of chipless machining method are forging, spinning, rolling, embossing and stamping. There are also other non-conventional machining methods that include the removal of material at very minimum levels-to some extent molecular levels. These too are part of chipless machining method. An example of such methods includes electrolysis. Some mechanical machining processes such as roller burnishing are also part of chipless machining method.
Always Evolving
The chip removal world is always evolving due to changes in mechanical technology. In order to improve the efficiency of machining tools, you often find that manufacturers are always trying to come up with versatile tools that offer efficiency and precision in metal cutting. This means that there are tools you can use to cut metal without having to carry a fleet of tools to carry out chip removal. Apart from achieving the desired shape and dimensions of the parent world, chip removal tools are tend to enhance the surface finish degrees as well as the dimensional accuracy. The challenge is machining is that when using the wrong tools, it becomes difficult to achieve the desired outcome especially if the shape is not easily implementable. This is the reason why using the right tool is paramount. In chip removal, the operations can either be implementing pieces with an axial-symmetrical shape or trying to implement any shape-even very complex shapes. However, the outcome is well dependent on the tools, process and super-finishing operations that are entirely necessary.