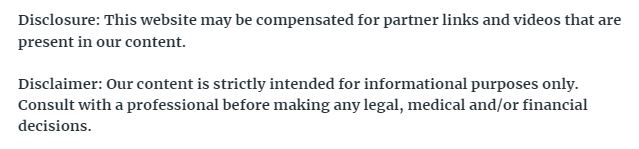

For thousands of years human lives have seen radical shifts in available technology that has forever influenced the social development of our species. Modern electricity, personal automobiles, and more recently the internet are all prime examples of how our lives have adapted thanks to breakthroughs in technology. While the products themselves are obviously at the forefront of such change, it is important to consider the developments needed behind the scenes in the form of machine tools that enabled the production and development needed to change lives.
Modern Machine Tools
The earliest machine tools were found around Egypt and Mesopotamia around the 3rd century BC in the form of hand-powered lathes. It was not until the Industrial Revolution in England when steam power and water wheels would be used to power such tools; in fact, the steam engine invented by James Watt actually required the development of accurately bored cylinders that was perfected by another inventor, John Wilkinson. Modern lathes and boring machines are just a few examples the wide variety of machine tools available today. The ancient hand lathe used over two thousand years ago has since been replaced by more accurate models like the Swiss-style lathe that provides unprecedented accuracy — this in turn paves the way for more intricate and complex feats of engineering and technology.
Intricate Parts
The advancement of machine tools is in many ways the culmination of thousands of years of human ingenuity. Taking a look at an average drill will reveal the presence of ER collets. ER collets are the most widely used clamping systems in the world. Manufactured from alloy spring steel that has been fully hardened, ER collets are ideal for a number of machining applications including milling, boring, reaming, tapping, and grinding. With the development of ER collets, machine tools are able to securely hold a work piece of varying sizes, allowing for an increased range of potential for users.
Professional Service
For all the modern developments of machine tools, it is important to keep in mind that they are still machines with moving parts that require regular maintenance in order to avoid break-downs and costly repairs. Experts recommend that workers constantly check oil levels to ensure that they are within safe parameters; in fact, all moving parts on a machine tool ought to be well lubricated — at the same time, any leaks in the system ought to be reported as this could be an indication of machine failure. Workers should be keen to remove excess material from machine tools to ensure that there is no clogging in the system. If at any time your machine tool begins emitting a strange odor or if it starts to make strange noises, cease operations and have a professional inspection done in order to avoid potential damages. Experts suggest having your machines professionally serviced at least twice per year in order to stave off the risk of breakdown. In some cases with neglected machine tools it may even be less expensive to purchase a new machine tool than it would be to keep up with repairs. In order to avoid repairs and ensure that your machine tools are performing properly, schedule regular maintenance schedules and ensure that employees are aware of how to care for these history-changing machines.