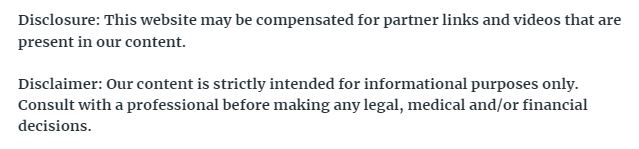
Stainless steel happens to be one of the metals that is used in a wide variety of industrial applications because of its corrosion resistance quality. Due to its availability in different types of stainless steel grades, you can use the metal in a wide range of applications. However, there is a great challenge for industrial applications where some professionals might be unaware of what is stainless steel, steel composition, stainless steel uses and stainless steel machinability. It is expected that any industry expert where metal is used should understand the kind of metal they are using in different applications. However, there is no guarantee that this knowledge is paramount across different people. What is important to understand about steel is that the metal if often referenced as if it was one single material. However, there are over 100 distinct compositions of stainless steel in use whereby each type is formulated to carry out a specific task. For example, there are certain types of steel that are used for tough industrial applications while others are used for aesthetics purposes. There are also types of alloys with stainless steel such as astm b584 silicon bronze that are best suited for fabrication operations and other machining purposes.
Why Stainless Steel is Upgraded
When it comes to upgrading stainless steel, the end product is supposed to be beneficial to both the manufacturer and the end user. For example, a metal such as astm b584 silicon bronze on its own might not be the best for complex industrial applications but when alloyed with other metals, it can effectively serve its purpose. One of the main reasons of upgrading stainless steel is to improve its heat resistance and resistance to corrosion. When you think about it, alloying stainless steel with astm b584 silicon bronze or any other composition with other metals can greatly improve corrosion from moisture, acids and other atmospheric conditions. In addition to this, upgrading stainless steel with astm b584 silicon bronze helps in improving the strength and durability of the end product. You can harden the entire metal or certain parts of the metal to improve its strength against aggressive environmental conditions. Remember, metals are used for that very specific purpose which is why they are common in the construction industry. Another reason of upgrading stainless steel is so as to reduce the metal’s maintenance needs. Homeowner and industrial users alike prefer a metal that does not require an extra coating as a way of maintaining it. Most users will prefer a metal that has low maintenance need since such maintenance is also an added cost to the user.
How to Choose the Right Stainless Steel for Industrial Applications
When it comes to choosing the right stainless steel for various industrial applications, there are a few factors that you need to take into considerations. Early uses of stainless steel included things such as the production and manufacture of cutlery, nitric acid tanks and gun barrels. As the industries continued to explore additional uses of stainless steel, there emerged the need to choose the right stainless steel grade that had better characteristics in terms of machinability, strength, corrosion resistance and strength levels. For example, type 304 stainless steel is one of the metals that is known to be used in various industrial applications that range from the manufacture of chemical plant equipment to cookware. However, this metal has many variations hence its wide use. When it comes to metal applications in marine environment, type 316 is the most preferred by many manufacturers and industry experts. Type 304 on the other hand requires low hardening work which is why it is the most preferred for cold-forming operations. From the analysis above, it is evident that choosing the right stainless steel grade is not always easy. Everything narrows down to the specific use of the type of metal you intend to use.