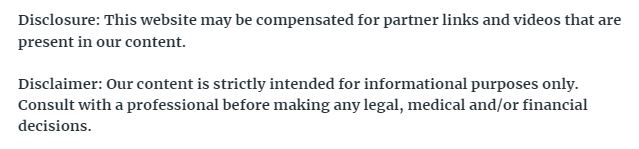
Load testing is a critical process in various industries, including construction, manufacturing, and maritime operations, to ensure the safety and reliability of lifting equipment. It involves applying a load to a piece of equipment to verify its strength and functionality under working conditions. Properly conducting load testing requires specific tools, knowledge, and adherence to safety standards. Here’s what you need for effective load testing:
1. Appropriate Testing Equipment
The core of load testing is the equipment used to apply and measure the load.
This includes:
Load Cells: These devices measure the force exerted during the test. They are essential for obtaining accurate readings of the load applied.
Test Weights: Depending on the type of equipment being tested, calibrated test weights may be used. These weights must be certified and accurate.
Hydraulic Jacks or Pulling Devices: These are often used to apply the necessary load, especially for dynamic testing where controlled force application is required.
2. Certified Testing Standards
Adhering to recognized testing standards is crucial for ensuring safety and reliability. Standards such as those from the Occupational Safety and Health Administration (OSHA), the American Society of Mechanical Engineers (ASME), and the International Organization for Standardization (ISO) provide guidelines on how load tests should be conducted. Ensure that your testing procedures align with these standards to guarantee the validity of your tests.
3. Skilled Personnel
Load testing should be conducted by trained and certified personnel who understand the complexities of the equipment and the testing process. These individuals should be knowledgeable about:
Test Procedures: Understanding how to set up and execute the test correctly.
Safety Protocols: Ensuring the safety of all personnel and equipment during the test.
Data Interpretation: Accurately reading and interpreting the results to determine if the equipment meets the required standards.
4. Safety Gear and Precautions
Safety is paramount in load testing. Ensure that all personnel involved wear appropriate personal protective equipment (PPE), such as hard hats, gloves, safety glasses, and steel-toed boots. Additionally, establish clear safety protocols and emergency procedures. This includes securing the test area, using barriers or caution tape to keep unauthorized personnel out, and having a first aid kit and emergency contact numbers readily available.
5. Detailed Documentation
Proper documentation is essential for maintaining records of the load testing process and outcomes. This includes:
Test Plans: Detailed procedures and objectives for the test.
Test Data: Recorded measurements and observations during the test.
Inspection Reports: Summaries of findings, including any discrepancies or failures.
Certification: Official documents certifying that the equipment has passed the load test and is safe for use.
6. Maintenance and Calibration of Testing Equipment
Regular maintenance and calibration of testing equipment are vital to ensure accuracy and reliability. Load cells, test weights, and other devices must be regularly inspected and calibrated according to manufacturer specifications and industry standards. This ensures that the testing equipment provides accurate measurements and reliable results.
7. Environmental Considerations
Consider the environment in which the load testing is conducted. Factors such as temperature, humidity, and weather conditions can affect the results. Ensure that the testing environment is controlled or that any environmental factors are accounted for in the test plan.