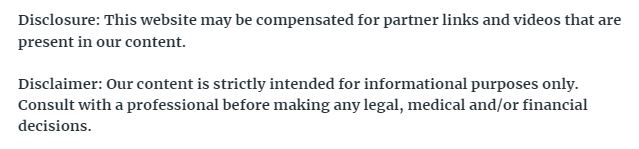

Have you ever get curious about how those plastics and glass items you use get manufactured? Maybe you already have the idea of the entire production process. But if you don’t, it’s wise to stick around. Generally, plastics and glass products are everyday essential for most people; whether you need them for storage, product distribution, organizing tools or any other purpose you might find, they simply serve their purpose right.
Yearly, the world produces and consumes roughly 600 billion pounds of plastic as the market still grows at about 5% a year. These are tons and tons of plastic materials made for different household and commercial use. Ideally, plastics and glass containers come in various shape, size, and colors. Their application also varies depending on the material used in manufacturing a particular that particular item. For instance, there are plastic containers specifically designed to store food products while others made to store and carry chemical substances. Regardless of their are of use, all these plastic chemical jars, and food containers begin from the simple and sophisticated art of blow molding.
In modern manufacturing, companies can now choose between three specific blow molding methods in making exceptional and quality plastic and glass containers. These techniques include stretch blow molding, injection blow molding, and extrusion blow molding. To understand how blow molding works, let’s have a look at these three molding processes.
Stretch Blow Moulding
Stretch Blow Moulding is a technique applied in making bottle, jars and similar blow molded containers. This process produces quality items of different dimensions. Here, the polymer needs to be injected molded on a ‘preform’ first, with its neck threads at one end. Then, at high temperatures, the preform is heated and blown into bottles. As this process continues, the preform is stretched and filled inside. Additionally, strain hardening is applied in the process to ensure these plastics and bottles don’t deform under extreme pressure caused by carbonated beverages.
Injection Blow Moulding
It’s interesting how blow molding works using this method. It’s, however, the least molding process used in custom bottle manufacturing like the production of small medical containers. This is because it has a slow and lower production rate than the other two molding processes. Typically, injection blow molding is used in making large quantities of cylindrical and hollow plastic object. In this process, a polymer material is first injected and molded onto a core pin that rotates towards a blow molding channel. It is then filled with hot air and left to cool
Extrusion Blow Molding
This is another functional blow molding mechanism and probably the widely used. It is used to process an array of polymers such as polypropylene, polyethylene, polyvinyl chloride among others. With the first step of this process being downward extrusion, tubes are designed to reach different lengths before the mold is closed. But before that, the neck end of the tube is gripped, and then a blown injector is inserted to inflate it. The final product is then ejected from the mold and any excess material is scraped from the bottle’s neck, side, and the bottom.
Basically, these three processes explain how blow molding works, and now you have an idea of what really takes to make a plastic object.