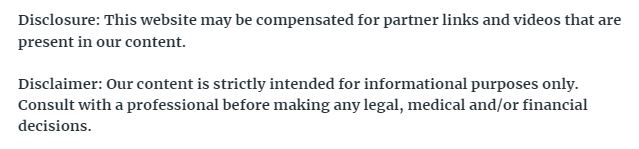
Among all construction materials the human race has ever used, metals rank highly. In fact, a few prehistoric eras are now named after the most commonly used metals of the time, such as the Iron Age and the Copper Age. By the Industrial Revolution, steel and forged metals were mass produced for the first time, which allowed for the construction of I-beams, railroads and trains, steam engines, and other marvels. This trend continues today, and induction furnaces are responsible for melting down iron and steel, aluminum, copper, and other metals for making a final product. Such melting furnaces feature tightly controlled temperatures, and an induction heating coil is typically made of tough metals and alloys so that it doesn’t accidentally melt itself. Now, what is there to know about induction furnaces and the metal forging industry today, and steel melting? What are steel, aluminum, and alloys used for?
It is safe to say that the modern metal forging industry is a robust one, and there is no end in sight. In fact, the Bureau of Labor Statistics believes that the sheet metal industry will grow even more in the coming years, and add a few thousand new jobs to the American economy. Induction furnaces, steel mills, and other metal melting furnaces make all this possible. In particular, the world’s crude steel production hit 1.69 billion tonnes in 2017, which is a 3.9% increase from 2016’s figures. The United States, Canada, China, and Germany in particular are known for their high steel output, and the U.S. in particular imports a lot of it. In 2017, the U.S. imported some $27 billion worth of it, and 17% of it came from Canada alone.
As for manufacturing methods, induction furnaces are essential. Such furnaces boast precise temperature controls, and they will not accidentally overheat the material and damage its alloy components. Instead, induction furnaces apply induction heating (hence the name) with electrical coils, and those heating coils are made of very tough metals and alloys such as tungsten, which have incredibly high melting points. So, the components stay safe when they create enough heat to melt iron and steel into molten metal. As for capacity, some induction furnaces are larger than others; some can handle one kilogram of material, and others, over 100 tonnes of it. This heating process is also clean and energy-efficient, though foundry staff should routinely look over the metal coils and other components to check for any problems. These parts are tough, but not immune to faults or wear and tear.
Steel can be either hot rolled or cold rolled, once it is forged. What does this mean? At first, the material is passed through a series of pressurized rollers at a high temperature, and this results in hot rolled steel. It has imprecise dimensions, but that is acceptable for uses such as making I-beams and railroad tracks. If that steel is passed through the rollers again, but at room temperature this time, the result is cold rolled steel. It boasts a protective finish and precise dimensions, useful for making a wide variety of items at workshops and factories.
Uses for Steel and Aluminum
These metal cannot perform literally every job; sometimes, alloys are needed. Still, steel and aluminum together can cover a lot. As mentioned earlier, steel is the go-to material for railroad tracks and I-beams since it’s light and strong, and it is vital for making car parts and metal roofs for houses. On a smaller scale, stainless steel is used to make surgical equipment and cutlery such as knives and forks. Some steel alloys can be used for these and similar jobs, with properties such as bolstered stain resistance or a tolerance for high temperatures.
Aluminum has its place, too. This metal is softer and lighter than steel, and now more than ever, it is used to make vehicle bodies for cars and trains, so the vehicle is lighter and therefore more fuel efficient. Aluminum is also used to make car rims. Meanwhile, many electrical devices and appliances feature aluminum parts, and in a tablet computer for example, aluminum is lighter than steel and tougher than plastic, making it ideal. Aluminum is also used for making power lines instead of copper, due to aluminum’s lower weight.