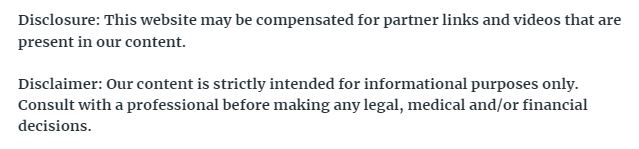
Surface finishing is an essential process that provides decorative and protective finishing to reactive metals and other assembled components and parts. Unprotected metals form rust when exposed to oxygen, losing their structural integrity and functionality.
The two metal coating types used for professional finishing are: powder coating and liquid coating. They both serve similar functions though each coating type has unique benefits as well as limitations.
Both coating types contain almost the same components: Resin, additives, and pigments. The only difference is solvent – which gives the liquid coating its wet characteristic.
Why Professional Finishing is Best Achieved with Powder Coating?
Powder coating is a popular dry finishing process that represents more than 15% of the total industrial finishing market. It’s a quick, efficient method and the best alternative to painting or liquid coating.
Health and Environmental Impact
Liquid coatings and wet paints emit high amounts of volatile organic compounds (VOCs). These are highly dangerous compounds that long exposure causes respiratory irritation and compounding health problems. VOCs also contribute largely to industrial pollution.
Because powder coatings are solvent-free, they don’t evaporate nor emit VOCs, and are completely environmentally friendly.
Performance
The performance of a coating is measured by how well it protects metal surfaces from corrosion and other environmental damage. Poor finishing makes it easy for surfaces to scratch and chipping, this compromises the coat’s effectiveness to serve as a protective barrier.
Professional finishing with powder coating performs much better than wet paint because of thicker layers and thermal bonding. It offers – more resistance to scratching, chipping and other wear and tear impacts. This performance makes powder coating ideal for outdoor products, like decorative bollards and bike racks.
Color Matching
In addition to providing superior performance and physical toughness, powder coating has excellent color retention. Even with long-term exposure to sunlight, powder coating still retains its original color because of high resin and pigment adhesion force.
The fading process due to long exposure to sunlight is referred to as chuckling. Mild chalking only causes the surface to fade slightly, but severe chalking will erode the coating reducing its surface protection. Powder coatings have exceptional chalk resistance, thanks to their resilient resin.
Textures
Professional finishing is nearly as important as performance in some applications. Both wet paint and powder coating can achieve desired textures, but others are easier to attain with a specific medium.
Powder coats make it much easier to achieve textured finishes. Thinner layers of powder coat are naturally textured, whereas thicker layers are smoother. Although powder coating can be used to achieve a high-gloss finish, liquid paint is far much easier.
Durability
Powder coating creates a long-lasting, strong, hard surface that is both protective and beautiful. Powder coatings protect a part or product against scratches, chipping, abrasions, corrosion, fading, and general wear by being more resistant to impact, moisture, chemicals, and extreme weather than most liquid coatings of equivalent thickness.
They can also be used as electrical insulators and can resist hundreds of hours of salt spray exposure. Colored powder coatings retain their brilliance and vibrancy even after being subjected to harsh situations. Powder coatings are well-suited for abrasive, high traffic, or high use areas due to their endurance, which reduces the need for future coating touch-ups or replacement.
Material Utilization
When it comes to powder coating application, almost all coating material is used. In liquid coating applications, the oversprayed coating is immediately lost to the atmosphere. But since powder overspray does not contain solvents, any undamaged or uncontaminated can be reclaimed and recycled for future coating applications.
While powder coating is a viable alternative to traditional liquid coating methods in terms of durability, performance, texture, color matching, specialized finishes, health, and environmental impact, some applications are still better suited to liquid coating methods. These considerations will help you decide if powder coating is ideal for your specific application.