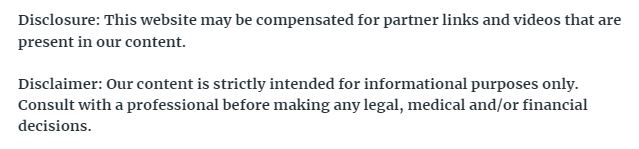
Despite today’s proliferation of wireless technology such as cordless phones and computer headsets, wires of all types are still integral to all kinds of electronics and the industries that use them. Computers, flat-screen TVs, heating and air conditioning systems, cars, and planes, among other things, need wires and cables to run, and the right sleeving for the job is vital for success. A cable or wire may also need crimpers to be ready for work, and some extremes of heat and pressure call for heat treatment fiberglass sleeving. What’s the right cable for the job?
Tough Cables For Work
Let us first consider the heavy stuff, cables and wires used for serious work. Some machines and appliances deal with extremes of pressure, tension, and most of all temperature during their operation, and the wires inside need to be protected. Heat treatment fiberglass sleeving is one such option. A car’s or airplane’s engine, for example, will run very hot, and wires need tough protection. Fiberglass weave is ready for the job, and there is a lot of work out there; it is believed that at any given moment, 9,728 planes carrying 1.27 million people in the air are operating, and those planes need the right parts to work. Heat treatment fiberglass sleeving can endure a hot engine’s temperatures, and it is tough enough to resist vibrations or abrasions during hard work. The cable may also be designed to minimize fiberglass dust when cut with scissors, to prevent a safety hazard. Ovens, toasters, and other heat-based appliances could also make use of this weave to keep their wires running safely.
Smaller, less heat-resistant wires also have their uses, whether on Earth or even in orbit. Satellites, for example, will need high quality wire work, given their essential jobs and the difficulty of reaching orbital satellites for maintenance. They don’t need heat treated fiberglass sleeving; instead, plastic sheathing on the wires is adequate, but the real question is if proper crimping has been done. A wire is useful once the last inch of its sheath at the end is stripped, and the bare wire is inserted into a crimp, or terminal, which allows it to interface with and connect to electrical devices and other wires. A hand crimp tool or an electric one squeezes the assembly together so that the inner wire is touching the crimp’s metal end and cannot be easily pulled back out.
Today, 24 GPS satellites orbit the earth, and communication with these devices is vital. In 1998, for example, 80% of the world’s pagers went silent when a Galaxy 4 satellite had trouble. Clearly, getting the right wire work done is key to making today’s electronics and global communication running smoothly. Any home built within the last 50 years is likely to have non-metal, or NM, plastic sheathing on its wires, a flexible and convenient material for home repair or for hired technicians to work with. This sheathing may be safer than metallic ones that have been used before.
Safety is another concern about wires. Electrical shock is the sixth leading cause of workplace deaths in the U.S., and every year, electric hazards claim 300 lives and injure about 4,000 more people. Heat treated fiberglass sleeving, when used properly, can maintain safety for any technician working on an engine or repairing an appliance, and proper crimping can handling of crimped wires can keep any worker safer. Replacing wires with worn-out sheaths and cables can also contribute to a safer workplace.