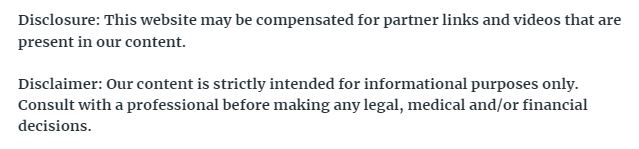

It very well might be a common assumption to make. The average Joe and Jane who are looking at particular low friction coatings may come to the conclusion that if they have seen one low friction then they have seen them all. Even though that might be a reasonable conclusion to some, it simply isn’t the way things are.
Industrial coatings are a big business. There were 352 million gallons of industrial coatings were sold to industries in 2014, alone. The cost to the customer industries was a whopping $6.8 billion. Friction coatings make up a great deal of that market.
When beginning to understand low friction coatings, it is a wise idea to consider what friction actually is. What do you have in mind when you are talking about friction coatings? Most in the coating industry see friction as the force between two bodies that keeps motion from occurring in an optimal way. Generally, there are two forms of friction: static friction and dynamic friction.
In basic physics, an object that is at rest is set in motion by forces that are acting upon that object. In static friction, those forces will act upon that resting object but the object won’t move at all. Typically, the static force is going to increase from the interlocking surfaces and prevent the relative motion from occurring. This will happen up to the point when some motion will occur.
When there are forces slowing an object down that is already in motion, this is called dynamic friction. I f the force can move the object, then it is called a dynamic condition. Another name for this is a kinetic condition.
You friction is going to come in all shapes and sizes. Sometimes you might be dealing with a frictional motion that is a rolling or a sliding. Typically, the frictional motion becomes what it is because of the surface. The surfaces might be very rough, have some deformities, or any other kind of defects that would cause the friction in the first place.
If you are calculating the coefficient of friction is might seem like a relatively simple calculation. You have the ratio of tangential and normal loads. The problem is, it can be a very complex parameter, completely dependent on the system.
If your friction is not very easily quantified, you might just be looking for some kind of qualitative improvement. You want to find the best coat for low friction. These are all considerations for when you are deciding between several different low friction coatings.
Hard coatings, like the metal coatings, and low friction coatings that are less hard, like thermal spray coatings and some wear-resistant coatings, have different properties that will meet the needs your equipment has. Over time, metal wear is going to occur. That is an inevitability.
Each year, metal wear costs industries all over the world millions of dollars, When the metal wears down without out any kind of low friction coatings having been applied, the replacement costs just skyrocket. In almost all departments, a loss is felt in a big way. The company cannot produce what they should, the need to repair and replace parts and components becomes great, and there is simply and overall loss of efficiency.
That wear happens when the friction is created. That static or dynamic friction–depending on the machine and its use–breaks down the metal on the machine and repair or replacement becomes necessary. To prolong that time between replacements and repairs, applying the correct low friction coatings can end up saving your company a great deal of money over time.
What you need to be looking for in your coating material is a nanocomposite that contains metal and diamond components. The metal is what makes the coating tough and the diamonds are the secret weapon. The diamonds give the coating a wear resistance that it wouldn’t otherwise have.
If you and your company are new to the world of low friction coatings, it is understandable for you to think that most hard coatings are the same, that there is not much difference. Take a look around and find the coating that’s right for you.