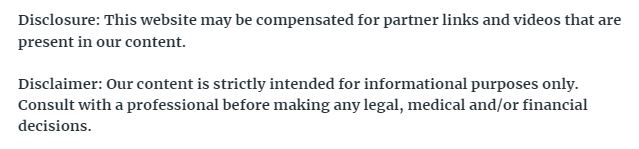
UPDATED 12/3/2020
The induction furnace technology is an alternative heating method to the conventional combustion furnaces and it’s known to offer superior performance and minimizes heat loss for both small induction melting furnaces and heavy steel shell furnaces. It’s a highly efficient in heating, melting, and alloying method used in casting different types of metals such as copper, steel, aluminum among other precious metals like silver and gold.
Induction heating equipment are designed with different capacities and frequencies to achieve varying production speeds and production.
Induction Furnace Inductotherm —Choosing the Best Induction Melting Furnace
If you’re in the metal casting business and want to improve your production, consider buying an induction furnace. But knowing which is the right heating equipment for your metal needs can be a daunting task. For this reason, you must do a thorough research on the types and brands of induction furnace available in the market, as well as find a reliable manufacturer who’ll help you make an informed decision on the type of induction furnace to buy.
Types of Induction Furnace Inductotherm – Core and Coreless Induction Furnace
Core type induction furnace is a low-frequency furnace and it includes three options, which are direct core, indirect core, and vertical core induction furnace.
- Direct Core Induction Furnace: This is a type of low-frequency induction furnace used to melt metals and it comprises a magnetic core, a primary winding, and a crucible. It looks much similar to a regular transformer but generally has a high-density flow of current. However, this furnace is more susceptible to loose couplings, which is a contributing factor to high leakage reactance and the best way to solve that is by operating the furnace at very low frequency. This type of furnace has now been rendered obsolete with the introduction of more powerful furnaces.
- Indirect Core Induction Furnace: Primarily relies on the principle of induction heating, this furnace has an iron core that connects with the primary and secondary winding. Connected to the AC is the primary winding which induces currents in the metal container attached to the secondary winding. In addition to metal casting, the furnace also provides heat treatment to improve metal properties. Unlike direct core induction furnace, this equipment offers more temperature control without having to depend on external control equipment.
- Vertical Core Type Induction Furnace
This is a much-improved version of the above core type induction furnace and it’s designed to use a vertical channel for the charge.
The induced currents allow the molten metal to circulate round the V portion while it doesn’t require much charge to ensure the secondary circuit remains closed. This is especially important as it greatly reduces interruption on the circuit. A vertical core type induction furnace is lined based on the charge. Since yellow brass has a higher corrosion resistance it’s ideal to use clay lining. For other types of metal alloys such as bronze and red brass, it’s recommended to use alumina.
Coreless Type Induction Furnace
This type of induction furnace inductotherm has three main components -the primary helical induction coil, a crucible formed from a refractory container and the frame. The key difference between this furnace and others is the absence of iron core. Small furnaces are built with preformed crucibles with the base and the walls made of ramming masses or refractory materials, which are heat resistance.
For large furnaces, the process is the same as for their small counterparts, only that a receptacle crucible is employed. Flexible cables are used for platform mounting while knife contacts are employed for floor level mounting. The coreless induction furnace is commonly used for the production of carbon-free ferrous alloys including alloy steels, carbon steels, stainless steels among others. With these types of induction furnace inductotherm technology, heating and melting metal is now made efficient with reduced heat loss and minimum material waste.
How Does Crucible Induction Furnace Work?

Crucible furnace has been used in foundry since it was first invented in India and central Asia. Crucible is the container where the material to be melted is placed, and it’s designed to withstand extremely high temperatures. The most common heating fuel includes propane gas, coke, and electricity. Propane gas is energy efficient and less expensive compared to an electric furnace. Propane gas is environment-friendly and does not emit toxins since when burnt, it only produces water and carbon dioxide. Hence it is safe to use and does not pose health dangers as opposed to other heating fuels. If you are a metal casting business looking for a heating solution that is affordable, durable, and reliable, 100k btu propane furnace and 80000 btu 80 furnace may be exactly what you need. While operating a furnace, the room’s temperatures are likely to rise, making the room uncomfortable to be in. Consider installing a 66000 btu air conditioner to regulate the temperature in the room.
Ensure you reach out to a professional who will advise you on the right furnace and the appropriate heating fuel that best suits your needs. If you settle for a crucible furnace as your absolute heating solution, consult a trusted manufacturer who will tell you about the advantages and disadvantages of a crucible furnace to make informed decisions.
Like this:
advantages and disadvantages of crucible furnace, air induction melting, industrial induction furnace, iron melting furnace, different types of induction furnaces, electromagnetic furnace, furnace definition wikipedia, how to calculate capacity of induction furnace, induction crucible furnace, induction furnace cast iron melting, induction furnace charge calculation, induction furnace cost, induction furnace diagram, induction furnace efficiency, induction furnace price list, induction furnace vs arc furnace, induction furnace working principle ppt, induction steel melting, melting loss in induction furnace, melting machine for steel, metal heating furnace.